Serial Number Making History Ii
I'll install the compact framework on my PC and see if I can figure that one out. Install clickonce programmatically scroll.
- •
- •
Model | Start # | End # | ||
Worcester | 1 | (1888) | 3,200 | (1898) |
Wonder Improved | unknown | (1895) | 41,000 | (1917) |
New Invention | 16,000 | (1910) | 23,000 | (1912) |
New Wonder Series I | 41,000 | (1914) | 143,000 | (1924) |
New Wonder Artist Special | 41,000 | (1917) | 237,000 | (1930) |
New Wonder Series II | 143,000 | (1924) | 237,000 | (1930) |
New Wonder Virtuoso Deluxe | 143,000 | (1924) | 237,000 | (1930) |
22M & 24M | 209,000 | (1928) | 237,000 | (1930) |
New Wonder Transitional | 237,000 | (1930) | 263,000 | (1935) |
Artist ('Naked Lady') | 263,000 | (1935) | unknown | (1971) |
Connqueror 26M & 30M | 263,000 | (1935) | 309,000 | (1943) |
Connstellation 28M | 330,000 | (1948) | 345,000 | (1952) |
Director 14M & 16M | 500,000 | (1955) | unknown | (1974) |
DJH Modified | 128,692 | (1980) | 221,243 | (1985) |
→ Full Conn serial number chart available. Click here to view.
Epiphone began in 1873, in Smyrna, Ottoman Empire (now İzmir, Turkey), where Greek founder Anastasios Stathopoulos made his own fiddles and lutes (oud, laouto).Stathopoulo moved to the United States in 1903 and continued to make his original instruments, as well as mandolins, from Long Island City in Queens, New York.
Charles Gerard Conn was born in upstate New York in 1844. As a 21 year old Civil War veteran, Conn invented a brass mouthpiece in 1874 for which patents were soon granted. The story goes that Conn devised his original mouthpiece after suffering a split lip in a bar brawl and, wanting to continue to play cornet in a local band, came up with a rubber rimmed mouthpiece ('a cushion for the lips,' Conn called it) that enabled him to play comfortably.
Serial Number Making History Ii The War Of The World
Having developed a process to vulcanize rubber to metal, Conn soon started manufacturing his mouthpieces, at first in humble premises over a drugstore in Elkhart, Indiana. In 1876, convinced that he needed specialist help, Conn persuaded a skilled French instrument maker, Eugene Dupont, to leave his employ at the Distin company in England and bring with him a small team of craftsmen. They subsequently formed the Conn-Dupont company, and started production of the Conn Four-In-One cornet, playable in four different keys. The Conn-Dupont operation lasted until 1879 when Conn regained full control of his company.
It was, in effect, these early events that would lead to Elkhart becoming the brass and wind capital of America, a position that it still holds today (the city produced some 60 per cent of all the wind instruments sold in the US in 1997).
Back in 1883 the Conn factory suffered a major fire, burning the building to the ground, but the city of Elkhart provided a large loan to help Conn back into business; Conn had been voted the city's first Democrat mayor three years earlier. Conn introduced the Wonder line of models at this time, and endorsers would include the famous wind bandleader John Philip Sousa, whose band was at one time kitted out with a complete set of gold plated Conns. Sousa later worked with Conn to design the sousaphone. Soon Conn claimed the largest factory of its kind in the world, employing some 300 workers (many of whom were brought to Elkhart from France and England). In 1886 Conn opened a second plant at Worcester, Massachusetts, in the former Fiske instrument factory; this lasted until 1898.
In 1888 Conn made the first US built saxophone, designed by Eduard A. Lefe/bre, and added saxophone models to its Wonder line, including soprano, alto, tenor and baritone. Born in 1834 in France, Lefe/bre was a clarinet virtuoso in his native country before his 20th birthday, and upon meeting Adolphe Sax fell in love with the saxophone and soon became a virtuoso on that instrument as well. Moving to the US in the 1850's, Lefe/bre joined Patrick Gilmore's famous 22nd Regiment Of New York brass band in 1873, and did much to popularize the still novel saxophone in the US. Gilmore's band usually featured a three man saxophone section playing baritone, alto and soprano. Following his collaboration with Conn in the late 1880's (it has been suggested, quite believably, that the Adolphe Sax instrument he brought with him to the US formed the basis of the first Conn saxophones), Lefe/bre also worked as a demonstration artist for Conn. After Gilmore died in 1892, Lefe/bre became the saxophone soloist in Sousa's band, a position Lefe/bre held until his own death in 1911.
In 1888, the same year that Conn introduced its first saxophone, the company's plant foreman Gus Buescher left to form the Buescher Instrument Co, and in 1907 Henry Martin's three sons left Conn to re-activate the Martin Band Instrument Co. Around 1900 Conn ran a short lived dedicated retail outlet in New York, and a patent for the new Conn Connqueror cornet was granted in 1901. Another fire, this one in 1910, destroyed another of Conn's factories, and a new plant was built nearby. At this time Conn dropped its Wonder line of instruments in favor of the New Wonder and New Invention models.
In 1915 Charles Conn sold his company to a group of investors headed by Carl Dimond Greenleaf, a successful flour mill operator. Conn himself netted $1 million, an enormous sum at the time, and retired to California. (The new owners added the abbreviation 'Ltd' to the company name, to make 'C.G. Conn Ltd' - a useful dating clue to identify instruments made before or after 1915.) Greenleaf expanded Conn, adding to the company a repair school, a proper assembly line, a research laboratory, and an organ production facility, and he laid the foundations for the US national school music programmes. By 1917 Conn had a workforce of 550 producing some 2,500 instruments per month.
Conn model names have included the Wonder, New Wonder, Connqueror and Connstellation lines, while musicians' own nicknames for Conn models have at various times included the 'Big Bore' and the 'Underslung' saxophones. Around 1919 Conn instigated a new model numbering system, with a letter indicating the instrument type - A for cornets, B for trumpets, H for slide trombones, M for saxophones - and an indentifying numeral preceeding this. Cornet model numbers include the 48-A (Superior Connqueror) and 80-A/85-A/92-A (Superior Victor). Saxophone model numbers include the 6-M (alto), 8-M (C-melody), 10-M (tenor), 12-M (baritone), 14-M (bass), 26-M (Connqueror alto) and 30-M (Connqueror tenor). Slide trombone models include the 6-H (Artist Symphony), 20-H (Connquest) and 40-H/41-H/42-H (Ball-room). Trumpet model numbers include the 4-B (Symphony, New World Symphony), 13-B (Aida), 15-B (Director), 22-B New Symphony) and 28-B (Connstellation).
Conn had introduced drawn-and-rolled tone holes to saxophones in 1919, based on a December 1914 patent by flute manufacturer William Haynes, and this made for better instruments than those with conventional soldered on tone holes. (Information concerning this patent is stamped on to many Conns made after this; the patent number 1119954 should not be confused with a serial number.) During the 1920's Conn dominated the booming saxophone business in the US along with its chief rival in the area, Buescher. By 1922 the company was turning out around 150 saxophones every day, and even introduced a a short-lived option of coloured lacquer that created saxophones in bright colours.
A number of Conn saxophones from this period are noted for their fine engraving work, often featuring a woman's portrait (known as the 'lady face' by players) and buildings in a landscape, as well as occasionally more ornate renderings. Talented engracers including Jake Gardner, Charles Stenberg and Julius Stenberg did this fine work at the Conn plant. While the company decided to stop using custom engraving at the end of the 1920's, Conn did continue to use several standard machine applied art deco patterns into the 1950's.
'Stencil' instruments were especially prevalent in the US saxophone boom of the 1920's, the term indicating the manufacture of instruments by one of the major makers - including Conn - stamped with a brand name to suit the customer. Thus Conn built saxophones and brass instruments bearing the names of Continental, Jenkins, Sears & Roebuck, Selmer (US), Wurlitzer, and York, among others. Conn also made their own cheaper brand of saxophones, Pan American. By the late 1920's the main Conn brand offered a line of saxophones that included Eb sopranino, C soprano, straight or curved Bb soprano, F mezzo-soprano, F Conn-O-Sax, Eb alto, C-melody, Bb tenor, baritone, and bass. However, by the calmer (and financially depressed) 1930's this was down to just the basic alto, tenor and baritone.
During World War II Conn effectively stopped instrument production and manufactured compasses, altimeters and other military related items. This, coupled with a long strike in 1946 and 1947, resulted in Conn's weak post war presence in the instrument market, although new lines did include the Connstellation brass models introduced around 1955. In 1949 Carl Greenleaf retired as Conn president, and the company, headed by Paul Gazlay in the 1950's, continued to founder. Piano and drum operations that had been purchased around 1930 were sold, and profitability generally suffered. Greenleaf's sons, Charles and Leland, fought for supremacy; Leland won and became president in 1958; Charles left for Buescher. Conn suffered during the 1950's and 1960's, slipping in relation to competitors, becoming inefficient internally, and struggling financially - although they did manage to produce Conn's one millionth brass instrument in 1963.
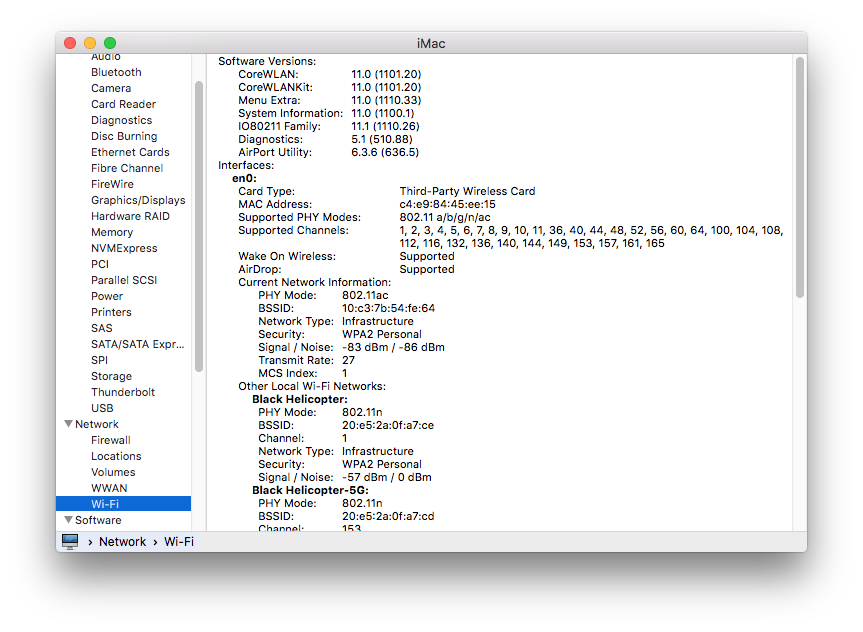
In 1969 in a hostile takeover bid C.G. Conn Ltd was acquired by Crowell-Collier Macmillan installed Jack Latter as president. Latter considered the existing production facility unworkable and suggested moving out of Elkhart. So Conn's Elkhart factories were closed in 1970 (the buildings were sold to Selmer US the following year), and from 1970 until 1986 Conn's brass and wind instruments were manufactured in Abilene, Texas, with student instrument production moving to Japan. Problems continued, this time because the new Texas facility took time to get underway and the new workforce was unused to wind instrument manufacturing. Instruments from this period are renowned for poor workmanship.1
No Conn feature pages were found in the database.
Have an idea for a feature page? Let us know! You can send info to SaxPics@SaxPics.com.
If you believe this to be an error, please contact corrections@SaxPics.com. Thank you.